Permanent Mold Casting Services
Get quality custom parts for prototyping and production, fast and cost-effective.
Permanent Mold Casting Materials
Aluminum | ||||
A356 | 383 | 413 | ||
360 | A383 | A413 | ||
A360 | 384 | B390 | ||
A380 | A384 | C443 |
* We can source any other materials.
Permanent Mold Casting Finishes
Standard. With no secondary processing.
Anodizing is an electrochemical process that converts the metal surface into a decorative, durable, corrosion-resistant, anodic oxide finish.
Aluminum is ideally suited to anodizing, although other nonferrous metals, such as magnesium and titanium, also can be anodized.
The bead blasting process shoots a blasting media – beads – under high pressure at a part to clean, polish, or roughen it to the desired finish.
A bead blast finish can clean a part’s surface, remove cosmetic defects, create a uniform surface with a dull, satin, or rough texture, and even harden a part’s surface and enhance its durability. It also prepares a part for paint and other coatings.
Bead media includes steel, glass, quartz sand, garnet, etc.
Manufacturers apply bead blasting for materials like metals, plastics, rubber, and glass.
Electrophoresis is the process of applying paint to parts by passing an electric current through the paint solution and parts immersed in it.
In many ways, this process is similar to electroplating. It is also called electrocoating, e-coating, electrophoretic coating, and electrophoretic painting.
Electrophoresis is suitable for aluminum alloy, zinc alloy, and stainless steel. It makes the parts present various colors and keep the metallic luster, and enhances the surface performance with high corrosion resistance.
Electroplating is the process of applying a thin layer of one metal to a part by passing a positively charged electrical current through a solution containing dissolved metal ions (anode) and a negatively charged electrical current through the part to be plated (cathode).
The aim is to improve the overall quality of the part. Some benefits include improving corrosion resistance, wear resistance, appearance, lubricity, and solderability.
Steels, nickel, copper-based alloys, and other metals are readily electroplated.
Polishing is the process of creating a shiny and smooth surface, either through physical rubbing of the part or by chemical interference.
The process enhances the aesthetic appeal, prevents corrosion, improves cleanability, and reduces adhesion of the parts.
It produces a surface with significant specular reflection but can reduce diffuse reflection in some materials.
Polishing works excellent with many metals, including aluminum, brass, stainless steel, and steel.
Powder coating is a process of applying a free-flowing, dry, thermoset, or thermoplastic powder to the surface of a part which is then cured under heat or with ultraviolet light.
The process creates a strong, wear- and corrosion-resistant layer that is more durable than standard painting methods.
It works perfectly on metals, plastics, and other materials.
Permanent Mold Casting Capabilities
Metric | Imperial | |
Max. Part Size | 800 x 800 x 600 mm | 314.96 x 314.96 x 236.22 in |
Min. Wall Thickness | 3.5 mm | 0.14 in |
Max. Part Weight | 80 kg | 176 lb |
Tolerances: NADCA Product Specification Standards
What is Permanent Mold Casting?
Permanent mold casting is a process in which molten metal is poured into a metal mold made from steel or cast iron to create new metal parts. The metal mold is called a permanent mold because it can be reused.
Advantages of Permanent Mold Casting
Can produce complex shapes and designs
Produces dense, regular castings by high dimensional precision
Excellent surface finish and grain structure
High production rate with low scrap loss
Low shrinkage and gas porosity
Improved mechanical properties of castings
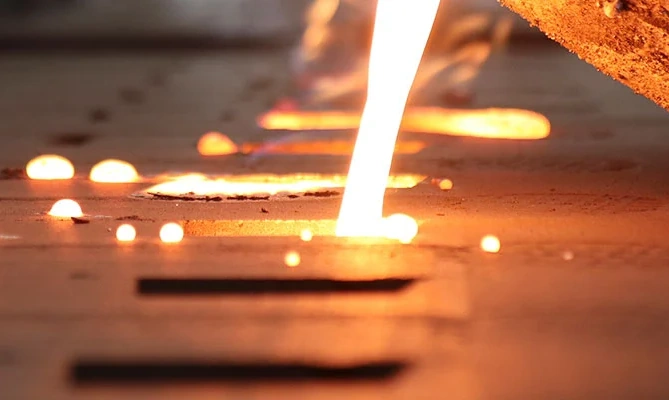
Permanent Mold Casting FAQs
Permanent Mold tooling can be expected to last 10,000 cycles, but often lasts 80,000 cycles or more.
The part density, complexity, configuration, thermal cycles, and cosmetic requirements can affect longevity. However, please feel free to ask us about your specific project, and we’ll provide as much information as possible.
Various parts like gears, engine pistons, pipe fittings, wheels, gear housing, etc., can be manufactured using permanent mold casting.
Common metals for permanent mold casting are aluminum, magnesium, and copper alloys. Metal like zinc, tin, iron, steel, and lead alloys are also cast in graphite molds.
Because of its ability to cast materials with high melting temperatures, common casting metals for sand casting are aluminum, brass alloys, and cast iron and steel.
How It Works
Get your parts with an easy 6-step process
Submit Your Inquiries
Get a Quote with Free DFM
Place an Order
Review Samples
Kickoff Production
Recieve Your Parts
Ready to Get Your Project Started?
Try our manufacturing services. We are committed to helping you fulfill your projects, from prototyping to production.